Pottery Firing: A Fascinating Journey from Clay to Creation
Pottery has been a timeless form of artistic expression and practical craftsmanship for centuries. The process of creating pottery involves various stages, with one of the most crucial being firing. Firing transforms raw clay into durable, functional, and aesthetically pleasing ceramics. In this blog, we will delve into the fascinating world of pottery firing, exploring the techniques, types of kilns, and the magic that happens inside these fiery chambers.
Understanding Pottery Firing
1. Bisque Firing: The First Encounter with Heat
The journey of pottery firing typically begins with bisque firing. After a potter shapes and forms their creation from raw clay, it undergoes a preliminary firing at a relatively low temperature. This process, known as bisque firing, removes any remaining water from the clay and prepares it for glazing.
2. Glazing: Adding Color and Texture
Once bisque fired, the pottery piece is ready for glazing. Glazes are colorful coatings applied to the surface of the pottery to enhance its appearance and functionality. The choice of glaze can significantly influence the final outcome, creating vibrant colors, glossy finishes, or unique textures.
3. The Kiln: Where Magic Happens
The heart of pottery firing lies in the kiln. Kilns are specially designed ovens that provide controlled and intense heat for the ceramic pieces. There are various types of kilns, including electric, gas, and wood-fired kilns, each offering distinct advantages and characteristics.
Electric Kilns: Commonly used for small to medium-sized pieces, electric kilns offer precise temperature control. They are convenient for studio potters and are often the choice for beginners.
Gas Kilns: Favored by experienced potters, gas kilns provide a more traditional firing experience. The use of gas burners allows for a reduced atmosphere, influencing the colors and textures of the glazes.
Wood-Fired Kilns: Embracing an ancient firing method, wood-fired kilns use wood as fuel. The flames and ash interact with the pottery, creating unique markings and patterns. Wood firing is a labor-intensive but rewarding process.
4. Firing Process: The Dance of Heat
The firing process itself is a carefully orchestrated dance of heat. The kiln is gradually heated to specific temperatures, allowing chemical transformations to take place within the clay and glazes. Different temperatures result in varied outcomes, from earthenware to stoneware or porcelain.
5. Cooling: Patience is a Virtue
Once the desired temperature is reached, the kiln is allowed to cool gradually. Rapid cooling can lead to thermal shock, causing the pottery to crack or break. Patience is crucial during this phase, as the cooling process can take hours or even days.
Conclusion
Pottery firing is a captivating journey that transforms humble clay into works of art. From the initial bisque firing to the application of glazes and the intense heat inside the kiln, each step contributes to the final masterpiece. Whether you are a seasoned potter or someone exploring the world of ceramics, understanding the intricacies of pottery firing adds a new dimension to the appreciation of this ancient craft. So, next time you marvel at a beautifully glazed vase or a meticulously crafted mug, remember the transformative power of the kiln that brought it to life.
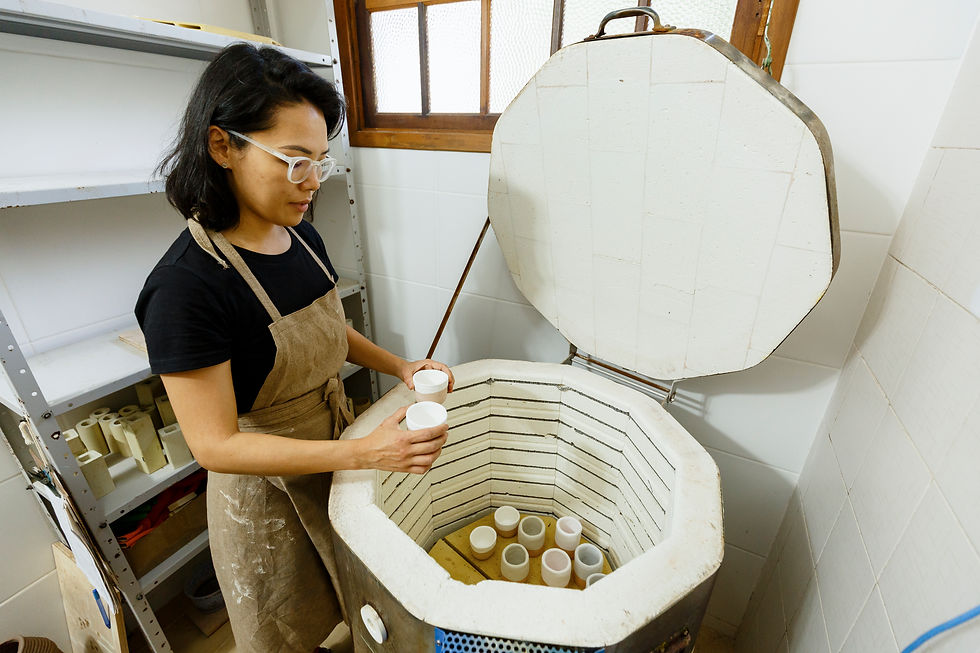
For the Ultimate Pottery Tool Kit visit www.sugarbushcreektradingcompany.com
Comments